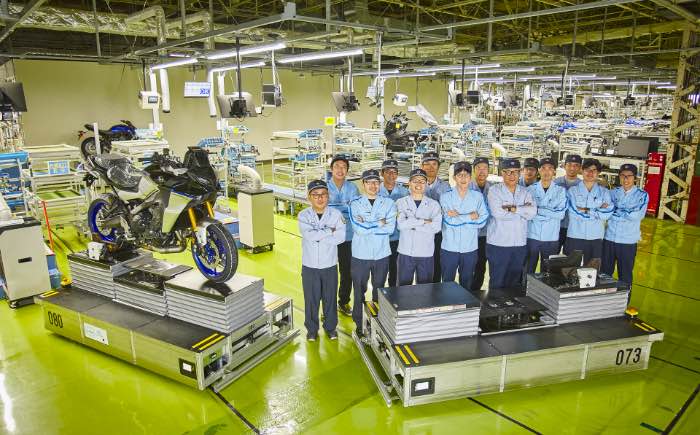
二輪車組立工場に於ける、新たなイノベーション「AGVバイパス方式」を確立したヤマハ発動機の生産課・組立技術部メンバー達
ヤマハ発動機は12月26日、車両組立の生産工程に於いて、135台の自動搬送車(AGV)を活用した「AGVバイパス方式」と呼ぶ全く新たな生産ラインの実用化を確立したことを明らかにした。
その新たな生産ラインの姿は、静岡県磐田市の本社オートバイ組立工場に於いて既に実現している。同拠点では、組立対象の二輪車を作業台を載せた自動搬送車(AGV)を複数連結することで旧来の生産ラインを代替。個々のAGVは、時には列を成して、時には列から外れて工場内を自動で走り続ける。
その様子を説明する生産工程の開発技術者の小林篤史氏は、「新たな生産システムでは、仕様の異なる複数モデルを同時・同一の生産ラインへ流す場合、各工程で組み付ける部品点数や作業時間が、それぞれ異なる場合であっても柔軟に対応できるようになっています。
例えば前に並んでいる車両が独自仕様であるため、他車とは異なる独特のまとまった作業時間を必要とする時や、逆に特定の作業工程自体が不要な車両であった場合、そのAGVは一旦、生産ラインの列を外れて、あらかじめ定められたプログラムの指示を受けつつ次の工程に自ら移動していきます。
このような生産ライン上の渋滞路を外れて、個々の車両組立のための最短の目的地へと直行する様子を称して我々は、この新たな組立ライン全体を〝バイパス方式〟と呼んでいます。
車両を載せたAGVは、人やモノの情報を携えて組立工場内を移動。作業者の身長や作業部位によって、リフターの高さや向きを最適化する
ちなみに、そんな新生産ライン〝バイパス方式〟が誇るべき優位性は、その見た目のシンプルさだけではありません。というのは、車両を載せたAGVは、それぞれの製品、それぞれの工程、それぞれの作業者が担うべき情報をも携えつつ移動するからです。
個々のAGVは、自らが向かう先々の工程に於いて利用するべきツールや、設備に対して組立情報の指示を出しつつ、個々のAGVを担当するべき個々の作業者の身長や作業部位を予め計算し、リフトの高さもそれぞれの作業者に合わせて最適化してくれるのです。
また突然舞い込んでくる1台の生産要請にも応えられるという対応力と柔軟性を併せ持っており、これらに係る個々のAGVのふるまいは、我々が長年、究極の多品種少量生産体制を目指してきた膨大な課題を解消させて、車両生産ライン自体の革命を実現するものなのです。
つまりAGVバイパス方式は、生産の効率化だけでなく、働き方改革や、省エネ等にも効果を発揮します。この新たな生産ラインは、将来のEV車両に応える生産を実現できるだけではなく、未来のモノづくりの多様化にも柔軟に対応できる旧来の生産ラインを超えた仕組みとなるでしょう。
これからは、この〝バイパス方式〟の導入によって組立工場の風景が、人がいきいきと働くスマートファクトリーへと大きく変わろうとしているのです」と述べた。
モノと働く人の情報を携えて工場内を移動。連結したラインから外れ、バイパスを通って次の工程に移動。製品はAGVから一度も降ろされることなく、完成検査場まで届けられる
また同じ組立技術部所属の技術者である曽貝健司氏は、「その様子は、次々と出荷場に現れる完成車だけを目にしていた場合は、もしかしたら単純な流れ作業のように映るかもしれません。
しかし、その規模感や変動する各種要件など極めて複雑な背景をご理解頂ければ、この流れるような生産現場がいかに高度な計算によって成立しているかを実感して頂けると思います。
そもそも意外に思われる方も多いと思われますが、オートバイは実は季節商品です。従って、需要変動に合わせて沢山の種類を少しずつ生産する〝多品種少量生産〟に応え続けなければならないという難しさが常に伴います。
同じものを常に同じ量つくるなら設備や仕組みをもっとシンプルにすることも可能ですが、実際の車両組立では、そうはいきません。
需要変動によってあるラインでは昼夜問わずフル稼働する一方、隣のラインは休眠中という非効率な状況が生まれてしまいます。また、生産ラインに携わる作業者にとっても変化が大きく、働きやすい職場ではありません。
例えば生産現場で扱うオートバイ部品の点数は、1日あたり約9,000種・計60万点にものぼります。一見、ダイナミックな印象を受ける組立工場ですが、実は繊細な計算の積み上げによって成り立っているのです。
そうしたなか5年ほど前には、8本もあった常設の車体組立ラインは、AGVバイパス方式の導入等によって現在までに4本へと半減しました。生産のDXの進捗によって、工場の姿は急速に様変わりしています。
これは、従来のコンベア方式に代わる画期的な生産システムです。長年に亘る課題を解消する革新的な設備として、今、大きな期待を集めている存在なのです」と結んでいる。