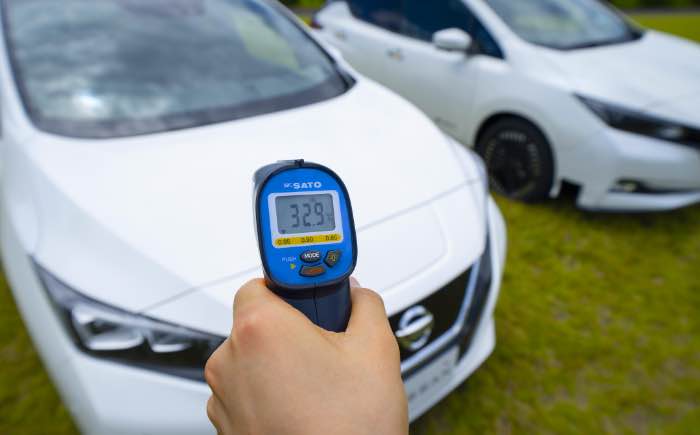
エアコン使用時、冷却速度が42%早く 商品化は特装車から
日産自動車は8月6日、夏場の燃費や電費向上に貢献する自動車用自己放射冷却塗装の実証実験を羽田空港内で公開した。実際に、同空港で実施している実証実験車両では通常塗装に比べ外部表面で最大12度、運転席頭部空間で同5度の温度低下を確認したという。(佃モビリティ総研・松下次男)
実証実験公開に先立ってプレゼンテーションした日産自動車総合研究所の三浦進先端材料・プロセス研究所主任研究員は自動車用自己放射冷却塗装について「開発した」とのコメントを肯定し、近いうちにも特装車から実用化可能との見方を示した。
そんな今回の自動車用自己放射冷却塗装は、米ラディクール社との共同開発製品だ。開発にGOサインを出した切っ掛けは、三浦氏が2017年科学雑誌「サイエンス」雑上で発表されたラディクール社( Radi-Cool / フィルム・塗料・布製品などを対象に放射冷却製品の開発を担う )の自己放射冷却に関する論文に感銘し、著者である米コロラド大学の楊栄貴博士( 米マサチューセッツ工科大学工科学院卒 )を尋ね、共同開発を持ち掛けたのが始まり。
その後、フィルム形態での冷却効果確認などを経て、2021年10月から塗料の共同開発に着手。これを踏まえ、2023年11月からラディクール社日本法人の販売代理店である日本空港ビルディングの協力のもと、ANAエアポートサービスが羽田空港で日常的に使用するNV100クリッパーバンに同塗料を塗装し、実証実験に乗り出した。
実証実験では、塗装の欠けや剥がれ、傷、塩害などの化学反応に対する耐性、色の一貫性、修復性などを検証。この結果、これまでのところ現時点で、問題がないことを確認。このように羽田空港内の過酷な作業に使用される車両で実施した実証実験で一定の成果を達成したことから、商品化の可能性を探り始めた。
自然界では通常みられない人工物質「メタマテリアル」を採用
日産では、まずはトラックや救急車など炎天下での走行が多い商用車の特装車への採用を検討する。というのも開発当初に比べ、自動車塗装で重要となる塗装膜厚は大幅に薄膜化したが、まだ量販車用と比較すると塗装膜厚は「6倍の厚み」(三浦主任研究員)であるためだ。
ゆえに大量生産体制を敷く量販車への適用は現状、実用的でないとし、特装車から採用を検討する。と同時に、一段の薄膜化の開発を並行して進める。
今回、日産が共同開発した自動車用自己冷却塗装は、物体の温度上昇を引き起こす太陽光(近赤外線)を反射するだけでなく、メタマテリアル技術を活用して熱エネルギーを放射するものだ。
より具体的には、一般に地表面から放出される過半の赤外線は大気に吸収される一方で、波長8μm~13μmの赤外線は大気をすり抜けて宇宙に放出される特徴を持つことに着目。
赤外線の波長を宇宙に放出されやすい波長に変化させ、熱を逃がしやすくする技術が、今回の車両用製品の開発に係るメタマテリアル技術の基礎となっている。
つまり、メタマテリアルとは「自然界に存在しない材料物性」であり、今回は「熱のメタマテリアル」として晴れた冬の夜間から早朝にかけて起こる放射冷却と同じ現象を人工的に引き起こす利用した格好だ。
これにより太陽光を反射するだけでなく、クルマの屋根やフード、ドアなどの塗装面から熱エネルギーを大気圏外に向かって放出することが可能となり、車内の温度上昇を抑制する。
日産は、このメタマテリアル技術が自動車用の塗料として活用できると考え、先の2018年からラディクール社との共同開発の可能性を検討。翌年の2019年にフィルムによる冷却効果を確認。2021年から塗装の共同開発をスタートした。
また併せて日産の純正アクセサリーでも、2021年11月発売の「サンシェード」や「カーサイドタープ」、「ハーフボディーカバー」にも同様の放射冷却効果を持たせたメタマテリアル技術が採用されている。
ちなみに自動車塗料への応用で課題となったのは、先の通り、放射冷却性能を確保するための塗膜の厚みの確保にあった。実はメタマテリアル技術の塗料は、既に建築分野で使われていたのだが、塗布には120µmの厚みを確保するべくローラーが使われている。
従って車両向けのエアースプレーを使った際の車両生産工程への適応性。更にトップコートとの相性、色の一貫性、塩害等の耐性、修復性など、自動車用塗料としての機能並びに親和性の確保にあたっては、およそ3年間程の時間が掛かっているという。
実証実験公開イベントでの質疑応答は次のとおり。
――今回、開発した自動車用自己放射冷却塗装の商品化のめどは。
「実証実験中であり、まだ商品化を発表できる段階ではありません。とはいえ、特徴が分かってきており、市販車でいえば商用車の特別塗装、いわゆる特装車への施工に向け、開発中です。と同時に、商品化に向けた開発も同時に進めています」
――実証実験の車両はどのような使われ方をしているのでしょうか。
「日常、物資を運ぶなど、空港内で過酷な使われ方をしている車両です。このため、常に日射にさらされている車両でもあります」
――量産化への課題は。
「量産車への採用に当たって、分かってきたことは、今回の開発中の塗装は厚みがあります。現状、通常塗装の6倍の厚みがあり、現時点で量産車への採用には厳しいものがあります。このため、量産車に向けた、塗装も開発中でありますが、お客様の要望により、特別塗装は可能であり、特装車への採用を検討しているところであります」
――製品、または製造工程での健康被害に問題はないのでしょうか。さらに電磁波が宇宙に与える影響はないのでしょうか。
「材料自体の健康への影響は、現状、ないと考えています。なぜなら、材料の中にある粒子は自然界のものです。放射される電磁波も日常、放射されるものと同じものです。ただ、その量が多く、熱を変えて外に持っていく性質のものです。地球自体も電磁波を放射しており、今回の電磁波はそれに比べて小さなものです」
――乗用車への採用は考えていないのでしょうか。
「乗用車へ採用するには、塗装の厚さがネックとなり、塗装膜が厚ければ塗装ラインが長くなります。ただし、考えていないわけではなく、塗装膜の一層の薄膜化の開発は進めています」
――薄膜化すれば冷却効果が落ちるのでしょうか。
「この材料には二つの粒子を採用していますが、薄膜化すればそのうちの近赤外線を反射する効率が下がります。一方で、放射冷却する分、通常の塗装より、冷却効果はあると考えています。このため、薄膜化の開発に当たっては、近赤外線の反射効率が落ちない粒子の開発、サイズや放射冷却効率がさらに高い粒子の開発などを進める考えです」
――冬の温度対応は。また、廃棄の問題はないのでしょうか。
「まず廃棄の問題について、今回の材料に入っている二つの粒子は自然界のものであり、廃棄上の問題はないと考えております。冬場については、これまでの検証結果、冷えません。なぜならば、放射冷却は温度の高さに比例して大きくなるからです。近赤外線の反射効果は一定です。実際、冬場に通常塗装のものと比較しましたが、ほとんど温度は変わりませんでした」
――塗装方法や耐久性については。
「通常塗装の上に、放射冷却塗装を施すこともでき、また直接、冷却塗装を行うことも可能です。耐久性でいえば、冷却塗装のうえに、通常塗装と同じクリアー塗料を施しており、耐久性は変わりません」
――燃費、電費効果はどのような比率になるのでしょう。
「燃費、電費はクルマと周辺の状況により、大きく異なります。参考値として、リーフを使った実験では、外気温が35度、エアコンの設定温度25度の条件で、通常塗装車との比較で時間が42%短縮されました」
――こうした冷却塗装について競合は。
「熱反射塗料については、自動車でも住宅でも、他メーカーから商品が出ております。しかし、自己放射冷却塗料については現状、我々以外に把握していません」