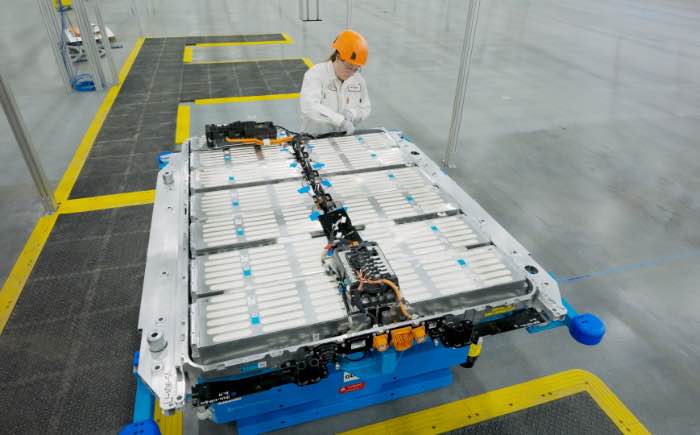
米国ホンダは2月3日(オハイオ州メアリービル発)、最新鋭EVの生産体制を確立させるべく、オハイオ州を拠点とするEVハブへの追加投資の増額する。
ちなみに日本のホンダ本社は2021年4月に、来たる2050年までに製品製造だけでなく事業全域からの二酸化炭素(CO2)排出量をネットゼロとすること。併せて2040年までに国際的な事業体制でBEVとFCVのみを販売するという経営計画を発表。
米国ホンダでは、この経営計画の柱をトリプルアクション・トゥ・ゼロのアプローチと呼んでおり、それは省エネやその他の環境に配慮した取り組みとなる。このトリプルアクション・トゥ・ゼロとは、カーボンニュートラル、クリーンエネルギー、資源循環という3つの行動領域を示して2050年までに環境影響をゼロにすることを目指す包括的な戦略を指す。
——————————————–
個々の3つの行動領域の詳細は以下の通り
——————————————–
カーボン ニュートラル:ホンダは2050年までに製品と事業からのCO2排出量を実質ゼロにする。今回ホンダEVハブ再構築では、天然ガスの消費量を削減するAEPの高効率溶解炉の設置が含まれる。
加えて設備投資にあたり、将来的にCO2排出量を更に削減できるプラズマアーク溶解に改造するべく新しい溶解炉を選択した。加えてカーボンフットプリントの削減をより確実にするため、全ての工場で新しい空気 HVACハンドラー、より効率的な照明、省エネ機器を導入する。
——————————————–
クリーンエネルギー:ホンダは、100%持続可能なカーボンフリーエネルギーを使用する目標を掲げており、再生可能な風力および太陽光発電に関する長期仮想電力購入契約 (VPPA) を通じて、北米の製造事業で使用される電力の60%以上を既に相殺している。
——————————————–
資源循環:ホンダは、製品を原材料に再加工し、その材料を新しい製品の製造に再利用することで100%持続可能な材料を使用することを目指す。このアプローチは、ホンダEVハブにも適用される。
——————————————–
またホンダは、AEPのアルミニウムを含む全ての工場で廃材をリサイクルしている。例えばアルミニウムは現場で溶解され、バッテリーケースやエンジンの製造に再利用される。そうした取り組みは従業員のユニフォームにも及び、これらはホンダとアキュラの自動車製造に使用するための吸音断熱材に姿を変えている。
これを前提に米国ホンダは、オハイオ州の既存の3工場( メアリーズビル組立工場<MAP>、イーストリバティ組立工場<ELP>、アナエンジン工場<AEP> )を米国に於ける未来戦略拠点と位置付け、これを「EVハブ」と名付けた。
今回は、このEVハブへの設備投資額を当初の7億ドルから10億ドル以上への大幅増額した。結果、盛り込まれる設備は、より柔軟なEV生産体制へと再構築していくことになるため設備内容も大きく刷新される。
その刷新策の骨子となるのは、生産ライン自体の組み換えであり、より具体的には、ICE、HV、BEVを同一ラインで製造できる体制へと再構築する。また人間に優しい製造プロセスを実現させ、持続可能な製造工程を採択することによってホンダの生産環境を大きく変革させていく構えだ。
個々拠点で刷新される設備は、例えばメアリーズビル組立工場でのライン自体の組み換えの他、バッテリー組み立てに於ける新たなゾーンの追加や、同社初となるCDC溶接の採用などが含まれる。アナエンジン工場では、バッテリーケースなどの鋳造用に6,000トン級の高圧ダイカストマシン6台を設置して更なる量産体制にも応えていく。
こうした設備の更新についてホンダ・デベロップメント・アンド・マニュファクチャリング・オブ・アメリカのボブ・シュウィン上級副社長は、「これはホンダにとって第二の創業だと捉えている。我々はこの機会を利用して、自動車づくりの方法論をゼロから再構築する」と述べた。
なおBEV生産では、2025年後半からアキュラブランドの新型SUVの「RSX」の生産を手掛けた後、2025年1月からは米CESで発表した「ホンダ0(ゼロ)」サルーンとSUVのプロトタイプをベースにした量産モデルの製造が開始される。
同様にバッテリー製造に関しても、オハイオ州ファイエット郡に設立予定としているLGエナジーソリューション(LGES)との合弁バッテリー工場「L-Hバッテリーカンパニー」に35億ドルを投資していく。なお同拠点の年間生産能力は約40ギガワット時(GWh)、生産の開始時期は2025年後半になる予定という。
——————————————–
最後に個々のEVハブでの刷新ポイントは以下の通りとなる
——————————————–
▶メアリーズビル自動車工場:
MAPでは2つの生産ラインを統合。ラインの大部分を撤去してICE+HVと同じラインでEVを生産できるようにした。この際、EVバッテリーパックを組み立てる世界初のホンダ工場という新たな責務に応えるべく工場の他のエリアも撤去した。これにより従業員が、効率的な稼働体制が可能となり生産ライン上に多目的なスペースも生まれた。
溶接作業の再構成では、MAPの2つの溶接ラインのうち1つを改造。新しい溶接ロボットと技術を導入してICEモデルと同じラインでEVボディを溶接できるようにした。結果、MAPで製造される全車両の品質を向上させた。
これには、EVモデル専用のフロアコンプにサイドシルを溶接する必要があったEVバッテリーケースを車両フロアに固定するための変更も含まれている。そそのために初めてCDC溶接も追加した。
既存の溶接ロボットに追加された同設備は、軽量で高強度の材料の使用を拡大させることに繋がり、それが製品の衝突安全性能を向上させ、車体フレームの重量を軽減することにも繫がった。
EV用バッテリーパックの組み立てでは、メアリーズビル自動車工場でのみ製造されるEV用のバッテリーパックを組み立てるための作業スペースを作るべく工場の一部を改装した。このプロセスで合弁バッテリー工場のLHバッテリーカンパニーのバッテリーモジュールと、アンナエンジン工場のバッテリー ケースメガキャストを組み合わせて、MAPとELPの両方でEV生産に使用される中型および大型車両用のEV バッテリー パックを製作。またバッテリーパックの組み立てでは、ホンダで最も長い無人搬送車 (AGV) ラインを使用する。
EV バッテリーパックの取り付けで、メアリーズビル自動車工場の生産ラインにはEVにバッテリーパックを取り付けるための専用エリアが新たに設置された。ICE車両とHVには、この新しいエリアを止まることなく通過できるため、それがマルチプラットフォームならではの柔軟性が発揮される。
ハイブリッドEVのバッテリー組立では、1つのラインで複数の車両タイプを生産する能力を増強させるべく、新しいハイブリッド バッテリーの組立エリアを設立した。それは車両組立ラインの設置エリア近くに移動され、ハイブリッドEVモデルに対する記録的な顧客需要に応えていく。
車両品質部門 (VQD)では、品質検査を強化した上でより人間に優しい機能を取り入れた。これにはEVや将来のソフトウェア定義車両 (SDV) の新しい安全性と接続性技術の調整と機能を確認するための新しい光学照準ステーションの改善が含まれる。
この変更により、ホンダ0シリーズ車両の新しいレベル3自動運転機能に必要なレーダーと光学照準の検証に対応。VQD担当者と車両に、より広いスペースが確保され、工場で生産される車両の品質検査を100%簡単に実施できる理想的なフローを実現させた。
スキルアップ面でMAPの従業員は、EV生産、EVバッテリー パックの組み立て、SDVの品質チェックに必要なスキルを身に付けるための新しいトレーニング プログラムを開始。これが安定した雇用と顧客の需要を満たす強力なチームの維持に役立っている。
——————————————–
▶イースト・リバティ自動車工場:
まずELPでは塗装部門の拡張に取り組んだ。そのために新しい塗装部門が建設され、エンジニアたちはその時間を活用し、重いEVボディ用に向き合うべくキャリアスキルを強化した。同プロジェクトには、完成間近のリン酸塩および Eコートの拡張が含まれる。この拡張により、ELPはより高品質の塗装外観を仕上げることにできる。
工場の北側には車両品質部門 (VQD) ビルを建設した。ここはMAPと同様に新しいオペレーションが導入された。それには将来のSDVの安全性と接続性を確認するための新たな光学照準ステーションが含まれる。新しいビルはVQDに係る組立と検査を行う従業員のためのスペースを拡張。同工場で生産される車両の品質チェックを簡単に実施できる理想的なフローを構築した。
組立部門のインフラストラクチャの改善では、ドロップリフト、コンベア、サポートビーム等、そされらの全てが強化・改善された。その他の変更では、最終組立ラインでのAGVを使用した新しいアプローチが含まれ、EV用のより強力で大型のボディキャリアも用意された。
メザニンではEVモデルをメインの組み立てラインから切り離した。その上で、EVバッテリー パックを組み付けられるようにするため特別なスペースが設けられた。バッテリー パックの取り付けが完了すると、EVは既存の組み立てラインに再び加わり、ICE及びHVモデルと共に共通ライン上で生産される。
溶接作業では、新たなEVに対応するためにMAP 溶接部門と同じ変更を行うことに加えて、ELP での溶接にも応えられるようにするため、既存のドロップ リフト、トランスファー、コンベア システムの強化と変更が含まれている。
——————————————–
▶アナエンジン工場:
AEPは40 年前にオートバイ エンジンの生産を開始して以来、同工場で生産してきた部品の長いリストにEVバッテリー ケースのメガキャスティングを追加した。これにはエンジンとエンジン部品、トランスミッション、カムシャフト、クランクシャフト、ハイテクCVT 部品が含まれる。EV バッテリー ケースは、ホンダとアキュラのEVのフロアのメイン フレーム構造として機能させる。
高圧ダイカストにも対応した。AEPはEVバッテリーケース部品の大型鋳造を行う6,000トンの高圧ダイカストマシン6台を設置した。これはホンダがこれまでにダイカストしたどの製品よりもはるかに大きく、2つの半分に分かれて作られ、AEPの後の工程で溶接される形となった。
これにより、ホンダは中型EVと大型EV用に2つの異なるサイズのケースを製造でき、ケースの半分は各サイズで共通になった。この巨大なプレス機は、ボディフレーム部品やICEまたはハイブリッド電気エンジン部品など他のアルミニウム部品を将来的に製造するための柔軟性を備えたものとした。
ダイカストマシンの設置には、高さ31フィートのマシンに安定した基礎を提供するために、工場床のコンクリート表面から80フィート下に支柱を設置するなど、工場を大きく改造した。
高効率天然ガス溶解炉の使用では、将来的にプラズマアーク溶解(PAM)に変更してCO2排出量を削減する可能性を念頭に置いて考えられた。これらの機械は、ICEおよびハイブリッド電気エンジンの製造に使用されている現在のAEP溶解炉およびダイカストマシンと比較して圧縮空気の使用量も削減できている。加えてプロセスから出るスクラップアルミニウムも100%リサイクルし、ケースとエンジンの製造で再利用できるようにした。
摩擦攪拌接合は、ホンダが世界で初めて量産に取り組んだもう1つの技術で、AEPは摩擦攪拌接合 (FSW) を使用してアルミニウム バッテリー ケースの2つの半分を接合させている。この技術は、溶接に必要なエネルギー量を削減させ、材料への熱の影響を最小限に抑える環境に配慮した方法を使用することで高強度の溶接が実現できている。
AEPでは、バッテリーケースの 2 つの半分を接合 (突合せ接合)。これにMAP でスタンプされるアルミニウムウォーター ジャケット (重ね接合) も取り付けるために新しい溶接技術を使用している。同ウォーター ジャケットは、バッテリー効率を最大化するために最適なバッテリーモジュール温度を維持するという重要な機能も併せ持っている。
写真測量法も活用した。具体的には各バッテリーケースの品質を迅速かつ正確に視覚的に分析するためにAEPでは、新しいマルチカメラマシンを使用して写真測量法を実施している。写真測量は、写真画像とパターンを記録、測定、解釈するプロセスを通じて物理的オブジェクトの信頼性の高い分析を取得する科学技術だ。AEPは2か所で写真測量システムを使用して100%の品質確認を実現させている。
ダイカスト工程の後、90台のカメラを搭載した4台の機械で部品の形状を視覚的に分析し、バッテリーケース表面の品質も100%の品質を確保した。また最終組み立て後、ケースをメアリーズビル自動車工場に出荷する前に120台のカメラを備えた2台の機械で各ケースを視覚的に分析し、MAPとELPでケースを車両フレームに取り付けることができるかどうかを確認している。
こうした写真測量機はもともと航空業界で利用されていたもので、品質チェックでは作業員が重いバッテリーケースを持ち上げたり、手作業でチェックしたりする必要がない、人に優しい工程を採用した。
最小量潤滑(MQL)加工プロセスでは、アルミ製バッテリーケース製造のエネルギー使用量を削減させ、部品の加工に必要な潤滑剤の量を減らす加工プロセスが初採用されている。この環境に配慮した製造アプローチは、優れた高品質の製品を持続可能な方法で提供するという取り組みを支えている。