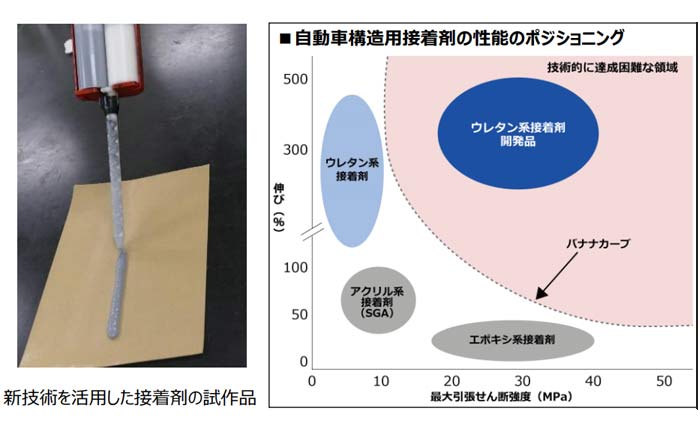
横浜ゴムは、自動車構造用接着剤の開発に活用が可能な、高強度と高弾性を両立した2液型ウレタン系接着剤の基礎技術を確立した。
今後、過酷なヒートサイクルにさらされる電子機器をはじめとした工業用接着剤など、多用途の接着剤開発に応用していく。
自動車業界では車体の軽量化が命題となっており、鉄鋼だけでなくアルミや炭素繊維強化樹脂(CFRP)などの軽量材料を組み合わせるマルチマテリアル構造が、欧州を中心に急速に実用化。マルチマテリアルの接合は溶接が困難なため、自動車構造用接着剤のニーズが高まっていると云う。
しかし、これまで使用されてきたエポキシ系接着剤は、高い強度を発現するが、動きに追従するフレキシブルな弾性が低く、多様な部材に対応しづらい面があった。
このため日本でも国家プロジェクトが発足するなど、マルチマテリアルに対応できる接着剤の開発が本格化。
こうした中、横浜ゴムでは、建築や自動車窓枠向けとして定評のあるウレタン系接着剤の技術をベースに、自動車構造用接着剤に求められる強度と弾性を兼ね備えた接着剤の研究を進めてきた。
今回開発した技術では、エポキシ系に匹敵する20Mpa~40Mpaの最大引張り強度と、ウレタン系ならではの最大伸び率200%~500%という優れた弾性の両立に成功。研究プロジェクトにおいては、一般的に達成困難な技術領域を定める技術的上限曲線(通称バナナカーブ)を越える数値を実現。
また、ウレタン系の弱点である温度、湿度といった環境による硬化の不具合や硬化速度の問題についても大幅に改善し、可使時間や強度発現を約2分~5分の間で設定できる短タクト性を実現。更に、硬化した後の接着剤の温度特性についても、従来のウレタン系接着剤と比べて-30℃~180℃の広い領域で温度依存性が小さい安定した物性を保持。動的な耐久性にも優れ、2液の混合比率のずれが最大±20%以内であれば強度、伸びともに変わらない品質の安定性を持つと云う。
また、混合比率を変えることで、物性の意図的なコントロールが可能、異種材料間あるいは接着部位に適した物性への調整もできるとのこと。
横浜ゴムでは、今後、同技術のさらなる検証を重ね、次世代の工業用接着剤として高い優位性を持つ接着剤の商品化を目指すとしている。