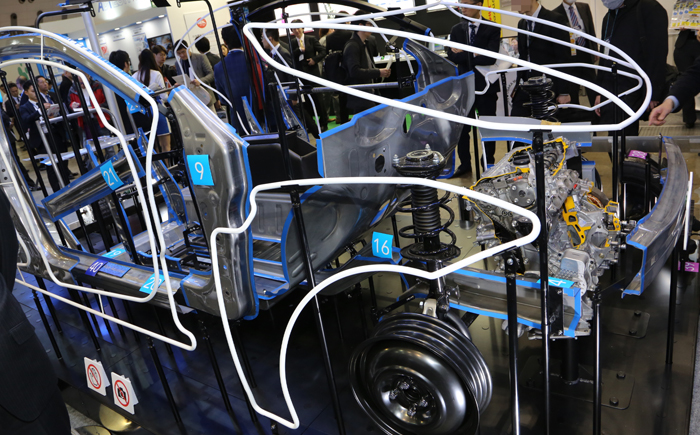
新日鐵住金は、「オートモティブワールド2019」(1月16日〜1月18日・東京ビッグサイト)内の「EV・HEV駆動システム技術展」にて、EVやHEVの骨格部品などに鉄鋼素材のみを使用しつつ、約30%の軽量化と衝突安全性の向上を実現する構造コンセプト「NSafe®-AutoConcept」を展示した。
近年、自動車部品は燃費向上やEVなどの航続距離を伸ばすなどの目的で、さらなる軽量化が望まれている。だが、一方で、衝突安全性などの向上も必要とされていることから、「軽さ」と「高剛性」という相反する要件を満たさねばならなくなってきている。
そのような時代のニーズに対するひとつの回答として、大手鉄鋼メーカーである同社が、長年の実績により多くのノウハウを持つ「鉄」を極め、最大限に素材性能を引き出すための部品構造やその構造を具現化する加工技術を組み合わせたのが「NSafe®-AutoConcept」だ。
展示ブースでは、同社が実際に試作した部品群を組み込んだデモ車両を展示。
例えば、フロントピラーの場合、1470Mpa鋼材という鉄を使用。これは従来品に比べ約6倍の強度をもたせながら軽量化も実現した部品だ。
一方でサイドメンバーは、1470Mpa鋼材と980Mpa鋼材を使用。事故などの時に変形し衝突エネルギーを吸収する必要があるため、剛性が高すぎないように約3倍の強度向上に留めている。
同社の担当者によると、このような強度の調整は「鉄はアルミと違い、最大7倍程度までは強度を自在に変えられる」という特性を生かすことで実現するという。
アルミ製部品は使う素材により強度がほぼ決まるが、鉄製の場合は、プレス加工時に曲げる箇所の順番を変えるなど、様々な方法で強度変更ができるというのだ。
また、バッテリーケースは、衝突などで凹みや歪み、変形などがあるとリチュウムイオンバッテリー自体が損傷し、最悪の場合は火災につながる危険性がある。
そのため、ケースを補強するバッテリーサイドフレームには、断面に独自の形状を採用することにより、衝突時もケース形状が変形しないような高い強度を確保することに成功。鉄ならではの高い強度と安全性の向上を実現している。
ほかにも、デモ機には、近年アルミなどが使われることが増えたフロントバンパーや、
トレーリングアームやロアアームなども鉄製部品を搭載している。
加えて、同社ではさらなる軽量化を目指すため、カーボンと鉄(一番右)や、チタンと鉄(中央と一番左)を組み合わせた複合素材による部品も開発中だ。
カーボンやチタンは、いずれも軽量で高い剛性を持つが高価であるため、一部の高級車やレース用車両などにしか使われないのが現状だ。
そのため、同社では比較的薄いカーボンやチタンに鉄を組み合わせることで、高い強度と軽さを両立しつつ、低コストも実現する部品の開発を進めている。
同社では、今後、このような鉄製部品の提供だけでなく、開発や車体設計などの段階から鉄を使った軽量化を実現するソリューションも事業化する予定だ。