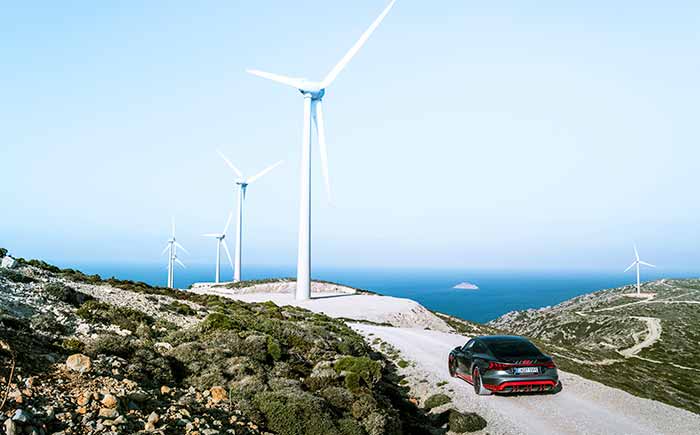
アウディは12月15日(ドイツ本国発表は12月9日)、電気自動車(EV)スポーツカー「Audi e-tron GT」の生産を、ネッカーズルムのベーリンガーホフ工場で開始したと発表した。同モデルはドイツ国内で初めて生産されるアウディの電気自動車となる。
100%グリーン電力と再生可能なエネルギー源によって生み出される熱を使用する同工場では、完全にカーボンニュートラルな方法で車両が製造される。資源の節約に配慮した工場内の車両製造プロセスでは、紙や梱包材の使用を削減し、アルミニウムおよびプラスチックのクローズドループを活用しており、さらに今回、製造プロセス計画段階において実車プロトタイプを使用していない。
アウディブランドのもっともパワフルな電気自動車であるAudi e-tron GTは、ハイパフォーマンスと高い環境意識を組み合わせたクルマ。そのクルマを生産する工場で採用された製造プロセスは、クルマ同様に非常にユニークといえる。アウディの歴史において、市販車の生産準備がこれほど短期間で整ったことはなかったという。
アウディの拠点では、既にプラグインハイブリッド車の生産に焦点を当てており、A6、A7、A8のプラグインおよびマイルドハイブリッド バージョンにより、アウディの生産拠点の中でも電動化モデルの割合がもっとも高くなっている。
■カーボンニュートラルな生産方法
持続可能なのは、このグランツーリスモの駆動コンセプトだけではない。ベーリンガーホフの生産プロセス全体が、完全にカーボンニュートラルなものになっている。2020年初めに、ネッカーズルムの生産拠点全体が使用する電力は、すべてグリーン電力に切り替えられている。
バイオガスを燃料とする熱電併給プラントが車両の生産において必要とする熱を供給。再生可能なエネルギー源の使用に伴ってどうしても避けられないCO2の排出は、認証を受けた気候保護プロジェクトのカーボンクレジットを使用して相殺されている。
AUDI AG生産およびロジスティクス担当取締役のペーター ケスラーは、アウディが掲げる「Missio:Zero」プログラムの中心的な目標について、ベーリンガーホフ工場は、ドイツ国内のアウディ生産拠点として初めて製造工程の完全なカーボンニュートラル化に成功した工場であり、これは2025年までに全世界においてカーボンニュートラル化を達成するためのステップだとしている。
「Missio:Zero」環境プログラムは、環境フットプリントを効果的かつ持続的に削減するための生産とロジスティクスにおける様々な対策から構成されており、その焦点は、脱炭素化、資源効率、生物多様性、水の使用に関する革新的ソリューションなどが含まれる。
■クローズドループによる環境保護
生産拠点において、重要な資源は節約され、原材料も現場でリサイクルされている。そのひとつが「アルミニウムクローズドループ」。Audi e-tron GTのサイドウォールフレーム製造の際にプレスショップから出るアルミニウムシートの端材を再利用するリサイクルチェーンを指す。
Audi e-tron GTのサイドウォールフレームは、絞り加工の最高点と最低点の差が35cmにも上り、それによってホイールアーチのショルダー部分に、quattroブリスターと呼ばれる特徴的で力強い造形が生み出される。
このプロセスを実現するため、最先端のアルミニウム加工技術を採用。アルミニウムクローズドループにより、切断後のアルミニウムシート端材はサプライヤーに戻され、リサイクルされてアウディが再使用する。これにより、ネッカーズルムの拠点において年間数千トンのCO2排出量が削減されているという。
環境に配慮したプロセスは、アルミニウムに留まらない。プラスチックのリサイクルでは、「古いものを新しいものに変える」という考え方を採用している。現在進行中のパイロットプロジェクトでは、A6およびA7の組立作業に由来するプラスチック端材は仕分けおよび裁断され、特殊な繊維に生まれ変わり、これらのフィラメントは、生産プロセスの3Dプリンターで使用される。
ベーリンガーホフ工場の社内3Dプリンティングチームは、各従業員の要件に合わせてカスタマイズされた多様な組立作業補助具の製造を担当しているが、Audi e-tron GTの製造には、こうした補助具が100以上も使われている。リサイクルプロジェクトの目的は、完璧なポリマークローズドループを創出する事だとしている。
■体系的なリソースの節約
Audi e-tron GTは、物理的なプロトタイプを製作することなく製造工程が計画された、最初のアウディ。現在、生産現場で実際に使用されているすべて組立手順は、社内で開発したソフトウェアおよびVRアプリを活用して仮想的にテストを受けたものとなる。
繊細なパーツの輸送に使用する専用コンテナの一部も、新しい仮想メソッドを使用してプロトタイプなしで製作された。これにより、金属だけでなく、部品を保護するためのパッケージも節約できる。ボディショップと組立ラインでは、メンテナンスアプリなどの新しいプロジェクトにより、ほとんど紙を使うことがなく、紙の節約につなげている。
ロジスティクス面では、デジタルラベルがテストされており、これが実現すれば、さらに紙の必要性が少なくなると考えられる。電子ラベルは、非常にエネルギー効率が高いだけでなく、変更があった場合に簡単に再プログラムすることもできる。
これは、従来の使い捨てラベルに比べて重要な利点となっている。。また、アウディのプロジェクトチームは、サプライヤーと共同で、梱包材の体系的なスリム化と廃棄物の削減につながるソリューション開発にも取り組んでいる。