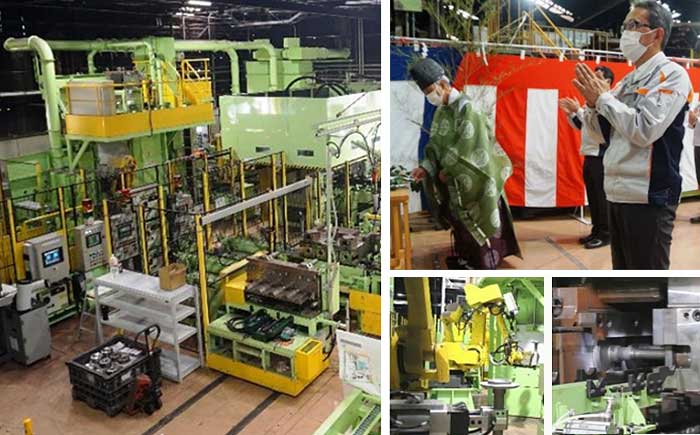
愛知製鋼は9月28日、自動車の駆動伝達部品の一つであるリヤアスクルシャフト(※1)を生産する新冷間押出し(※2)ラインの竣工式を同日執行し、稼働を開始したと発表した。
新たな新冷間押出しラインは、安全に作業ができるモノづくりの現場や、省スペースでの高い生産性、それに伴うCO2排出量低減や廃棄物ゼロ化による環境負荷低減を実現する、シンプルでスリムなものになっていると云う。
<新ラインの改善点>
【生産性】
・バッチ処理から1製品ごとの連続した表面処理とし、リードタイムを大幅短縮。
・重厚長大な設備から、製品を一個ずつ流す省スペースな設備への変更により、20%の生産能力向上かつ、13%のCO2削減。
【安全性】
・一部手動で行っていた作業を、AI画像認識やロボットの活用により完全自動化。
・機内で実施していた金型交換作業を、機外で実施できるよう改善することにより、やりにくい作業を無くし、安全性を向上。
【環境】
・従来の潤滑技術(ボンデ処理)を刷新した新技術「一液潤滑(※3)」により、産業廃棄物の処理を無くす。
愛知製鋼は、電動車の普及拡大によりエンジン部品の減少が見込まれる一方で、リヤアクスルシャフト等、駆動系部品に関しては、引き続きグローバルや国内物流業界で普及が進む大型電動車等への需要が見込まれるとして、今後も一層の安定品質・安定供給を図ると共に、地球環境に配慮したモノづくりで社会に貢献していきたいとしている。
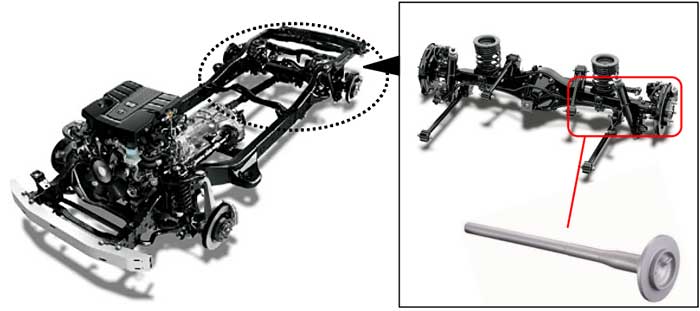
写真左:ラダーフレーム/右:リヤ部分(上)とリヤアクスルシャフト(下)。
※1:ディファレンシャルギヤ(自動車の左右の車輪に回転差を与えてスムーズに曲がることができるようにする部品)から駆動力を後輪に伝える部品。トヨタ自動車の新型ランドクルーザー(8月2日発売)をはじめとした大型SUV、ハイエースなどのミニバン等、グローバルで需要の高い車種に搭載。
※2:常温で材料(鋼材)を押し出して成形する技術。熱間鍛造よりも高精度な成形が可能。
※3:材料を化学的に反応させる従来のボンデ処理に比べ、材料に塗布するだけで素早く優れた潤滑処理を行える技術。使用後の潤滑液は産業廃棄物処理が不要で環境にも優しい。
[設備概要]
– 名称:リヤアクスルシャフト冷間押出しライン
– 設置場所:愛知製鋼鍛造工場内(東海市新宝町)
– 構成:冷間押出しプレス、ショットブラスト、冷間前潤滑装置、超音波探傷機。
– 生産能力:8万4千個/月
– 投資額:5億3千万円
※タイトル写真:左:冷間押出しライン(全容)/右上:竣工式の様子/右下:AI とロボットの活用で完全自動化。