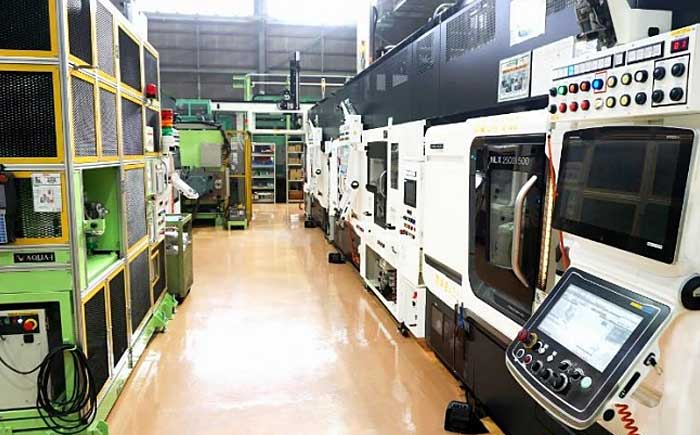
愛知製鋼は1月20日、電気自動車(以下、xEV)用駆動ユニット「eアクスル(※1)」向けの新部品(アウトプットシャフト)生産ラインを、鍛造工場内(東海市新宝町)に立ち上げ、その竣工式を同日開催、その稼働を開始したと発表した。
愛知製鋼では、2050年のカーボンニュートラル実現と将来の生き残り戦略の一環として、今後需要増が見込めるxEV搭載部品の新規開発と量産体制整備を積極的に推進。
今回、航続距離を伸ばすための高強度・軽量化や、静粛性確保(ノイズ低減)のための高精度化が強く求められるxEV向け部品には、同社が培ってきた高い鍛造技術が不可欠であるとして、最新鋭の“eアクスル向けアウトプットシャフト新生産ライン”を立ち上げた。
[新生産ラインの特長]
1.長年培ってきた高度な鍛造技術
中空形状の長軸部品に、冷間鍛造により内径スプライン(※2)を精密成形することで、材料の無駄を出さずに高強度・軽量化、高精度化を実現。
2.顧客ニーズに応える設計品質
従来顧客が行っていた複雑な機械加工工程を集約し、より完成部品に近い、高付加価値な製品を提供。
3.一貫ラインによる競争力強化
機械加工(切削)・冷間鍛造(※3)・機械加工(仕上げ)・検査工程を整流化。全自動一貫生産ライン(※タイトル写真)で、リードタイムの短縮および物流コストを削減。
愛知製鋼は、今後も、長年培ってきた鍛鋼一貫技術と最新の機械加工技術を活かし、顧客ニーズを先読みしたタイムリーな技術開発と生産体制構築を進め、xEVの普及拡大に貢献していくとしている。
※1:従来のガソリンエンジンに替わるxEV向け動力システム。トランスアクスル、モータ、インバータが一体となっていることが特長。
※2:円筒形の製品の内側に刻まれた歯型のこと。今回の製品では冷間鍛造によって歯型形状を成形。切削による成形よりも歩留まり・強度に優れる。
※3:プレス機を用い、再結晶温度以下(常温~300℃程度)で材料(鋼材)を鍛造することで成形する技術。熱間鍛造よりも高精度な成形が可能。
[設備概要]
– 名称:eアクスル向けアウトプットシャフト新生産ライン
– 設置場所:愛知製鋼鍛造工場内(東海市新宝町)
– 設備構成:冷間成形機、機械加工機、検査設備など
– 生産能力:2万個/月
– 投資額:4億5千万円